Objective
The objective of this WP is to coordinate the development and demonstration of multiscale predictive modelling techniques and diverse tools between the different WPs to ensure the integration into a digital representation of the physical system, an adaptive blade model. The goal of the adaptive blade-modelling tool is to predict accurately the structural performance in different length scales under consideration of manufacturing deviations and defects based on measured material properties, manufacturing parameters and operational events.
Description of activities and methods
The objective of this WP is to design an adaptive blade-modelling tool, which can create a high-fidelity blade model based on the real, actual physics of an analysed subcomponent/blade and its components based on diverse information such as scanned geometry, manufacturing deviations, defects and measured material properties. Moreover, the adaptive blade-model should not only be able to update the blade geometry and stiffness parameters at all-time but rather have the chance to generate blade models on different level of discretization and element type (super-element, beam element, BECAS input, shell, solid etc.).
Moreover, the implementation of selected fracture mechanics and damage mechanics modelling approaches into the adaptive blade-modelling tool will be part of the activities in this WP. The models should be able to predict the failure mode and to study the effect of the process-induced defects.
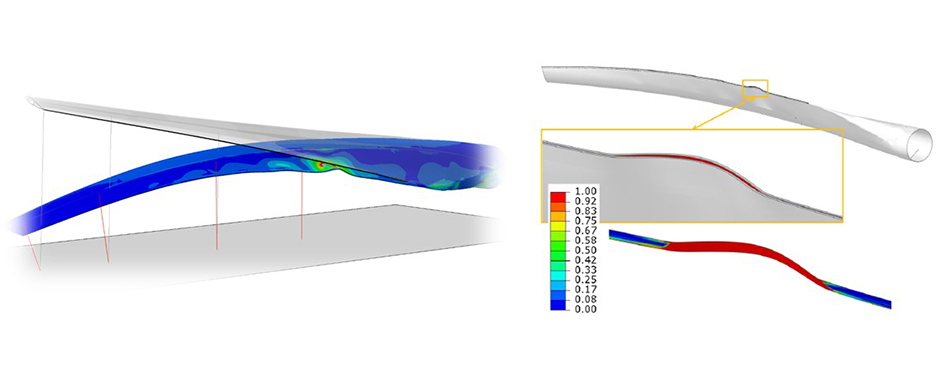
Based on implemented degradation models, the lifetime prediction of subcomponents and wind turbine blades and the validation of its prediction capabilities will be demonstrated. For this purpose, damage in structural blade models has to be modelled and compared to the effects of artificially created damages in the tested blades as well as to occurring damages due to manufacturing flaws or loads.
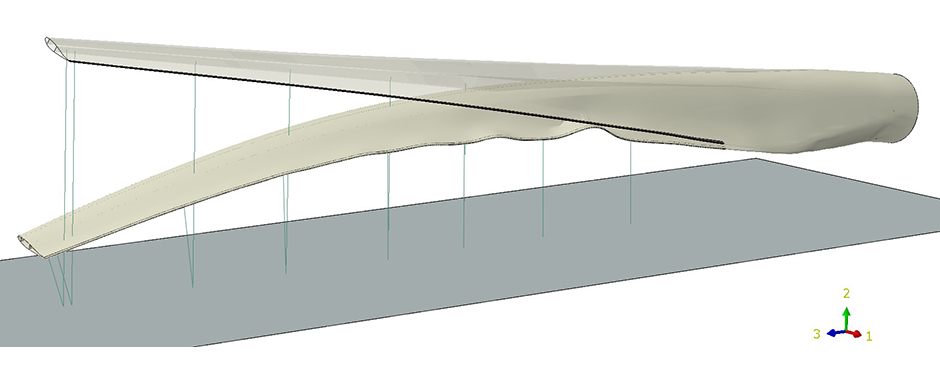
Finally, the adaptive blade-modelling tool will be integrated into the digital platform and based on the outcome of the activities in WP9, recommendation of multiscale modelling approaches for certification bodies will be suggested.
Work Package Leaders/Contact
Philipp Ulrich Haselbach