Objective
This work package demonstrates the predictability and efficiency of the Digital Twin concept in DTU Large Scale Facility by integrating the developed numerical models and monitoring, sensoring techniques and non-destructive testing (NDT) methods.
In total, three 12m blades (produced by Olsen Wings A/S) and two 40m blades (produced by Fraunhofer IWES) will be tested in full scale under combined bending and torsion in static tests and under bi-axial fatigue using exciters developed at DTU. Damage progress will be predicted, monitored and analyzed during these tests.
Description of research activities
- We manufacture all blades with embedded artificial defects which become damage when the blades are under cyclic loading.
- The damage types include delamination due to laminate wrinkles, adhesive debond in trailing edges, shear web/spar cap joints, inter-fiber fiber failure, etc.
- We instrument the blades with different censors and measurement systems, such as strain gauges, accelerometers, acoustic emission sensors, thermography, digital image correction.
- We monitor the damage progress of each damage during cyclic loading, for example using AQUADA techniques developed at DTU.
- We predict the damage progress of each damage during the cyclic loading, for example using FASTIGUE method developed at DTU.
- All test data are handled by a digital platform.
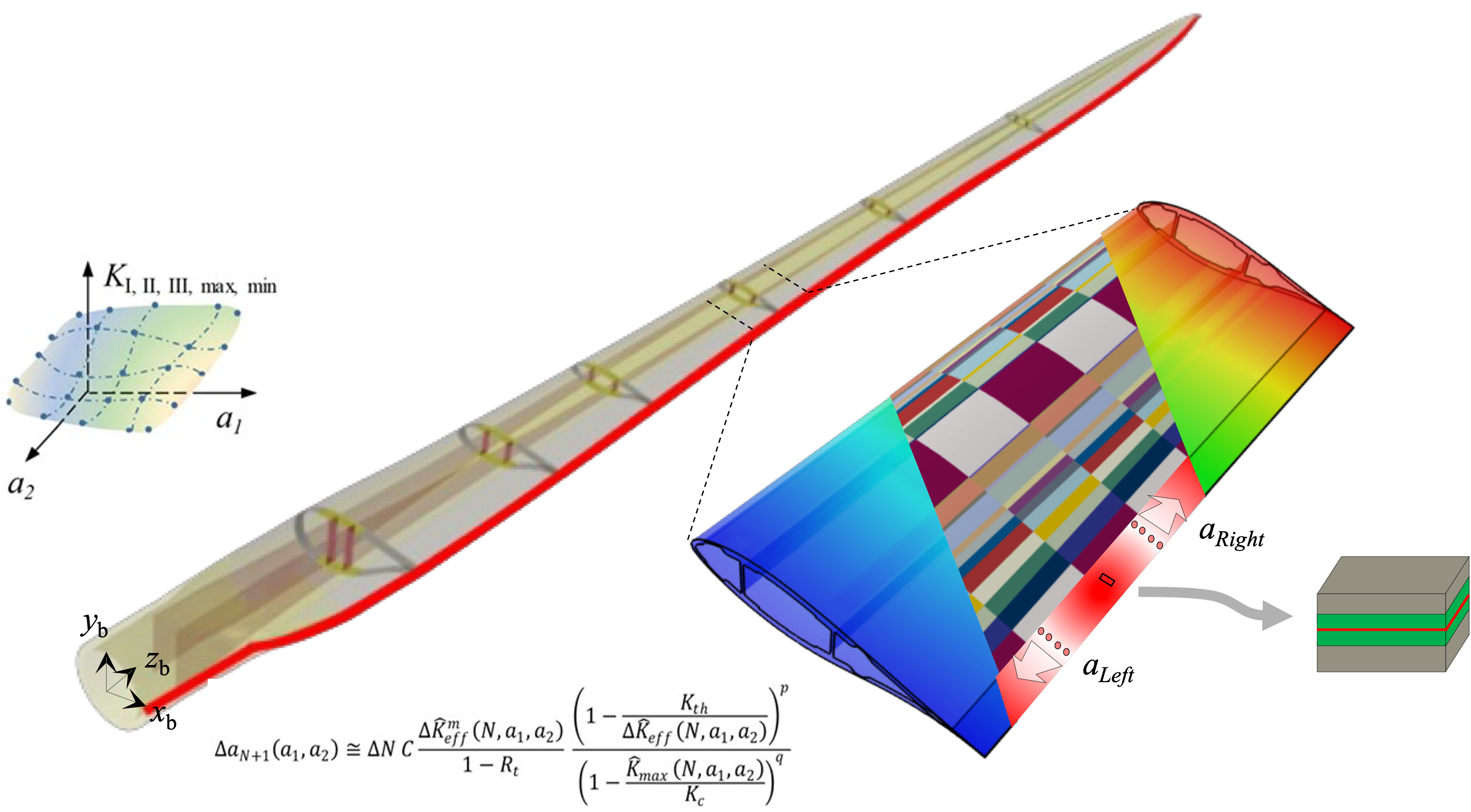
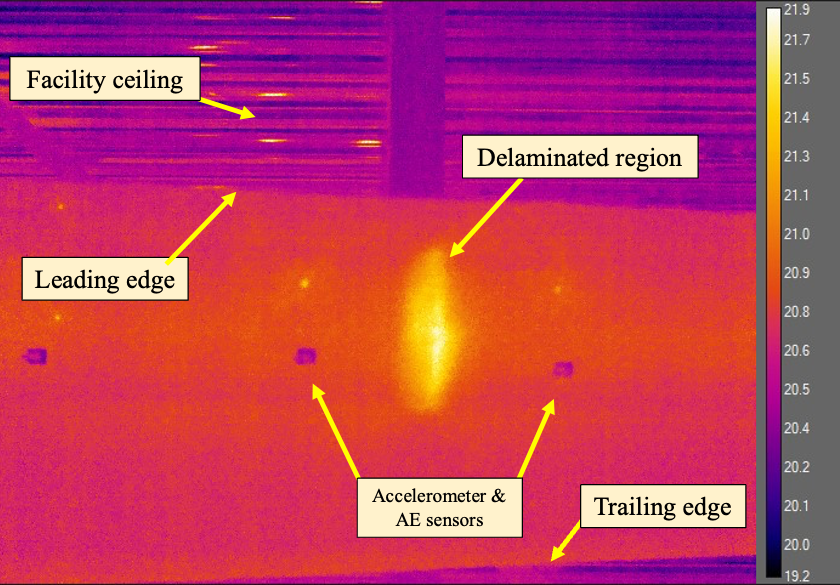
Work Package Leaders / Contact
Xiao Chen, Willi Wroblewski